Производство декоративного камня на основе портландцемента
Общие сведения об искусственном камне
Искусственный камень — это современный декоративный облицовочный материал. Высокий спрос на него обусловлен следующими факторами: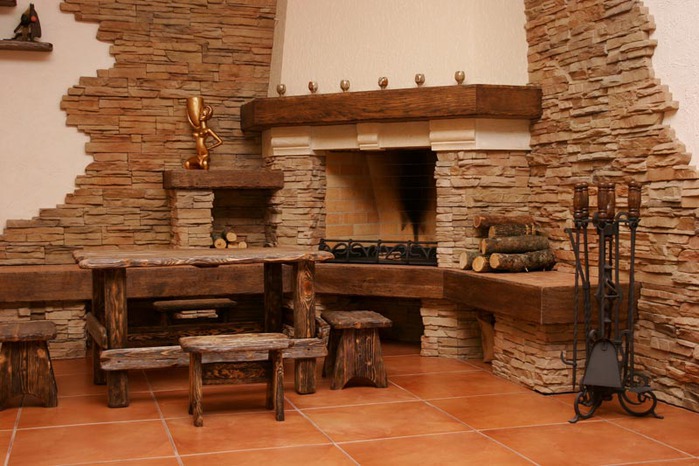
— высокие декоративные качества;
— простота и удобство укладки;
— огне- и влагостойкость;
— низкий вес (по сравнению с весом натуральных камней);
— низкая стоимость.
Искусственный камень не требует особого ухода и может прослужить без изменения цвета и фактуры не один десяток лет.
Применение современных технологий при производстве искусственного камня позволяет с удивительной точностью копировать фактуру гранита, базальта, песчаника, и других камней, изготавливать облицовочные плитки таких цветов и фактур, которые не существуют в природе.
Почти все оборудование, применяемое при изготовлении искусственного декоративного камня — такое же, как и при изготовлении тротуарной плитки (вибростолы, растворосмесители, весовое оборудование), за исключением одного — вместо жестких пластиковых применяются эластичные формы , которые являются ядром технологического процесса и самым важным производственным элементом.
Обычно облицовочные изделия из искусственного камня изготавливают размером — от 5 см2 до 0,5 м2 при толщине 1 — 2 см. В то же время плитки, имитирующие «булыжник» и «дикий камень», могут достигать толщины в 10 см.
В настоящее время искусственные камни изготавливаются в основном методами гиперпрессования, вибропрессования или вибролитья.
Данное руководство описывает процесс изготовления искусственных камней методом вибролитья, так как он, по сравнению с другими способами, позволяет изготавливать разнообразную продукцию высокого качества при сравнительно невысоких материальных затратах на организацию производства.
Ингредиенты бетонного раствора
Обычно состав бетонного раствора для изготовления искусственного камня включает в себя:
— портландцемент (белый или серый);
— вода;
— песок;
— различные наполнители;
— армирующие добавки;
— цветные пигменты;
— модификаторы (пластификаторы, ускорители твердения).
В большинстве случаев искусственный декоративный камень изготавливается на основе белого или серого портландцемента, что, в свою очередь, позволяет использовать такой камень для облицовки как внутренних, так и внешних поверхностей зданий и сооружений.
Нормальное твердение цемента происходит при температуре 15-20°С. Начало схватывания портландцемента должно наступать не ранее чем через 45 мин после затворения водой, а конец — не позже чем через 12 ч. При температуре от 0 до 5°С скорость набора прочности понижается в два-три раза, а при отрицательных температурах — почти полностью останавливается (так как вода переходит в кристаллическое состояние).
Прочность затворенного цемента нарастает неравномерно: за первые три дня она составляет 40-50% марки цемента, за 7 суток — 60-70% и только на 28-е сутки цемент набирает марочную прочность.
Белый портландцемент изготавливают путем измельчения белого маложелезистого клинкера, активной минеральной добавки и гипса.
Скорость твердения белого и цветных портландцементов несколько ниже, чем у обычных портландцементов, кроме этого у них повышенная усадка, пониженная морозостойкость и коррозионная устойчивость.
Вода — это то вещество, без которого увеличение прочности цементного камня невозможно. С другой стороны — излишнее количество воды, затворенное в растворе, отрицательно сказывается на прочностных характеристиках готовых изделий.
Поэтому при производстве искусственного камня следует, с одной стороны, обеспечить минимально возможное количество воды в растворе, а с другой стороны — создать необходимые условия для обеспечения процесса набора прочности готовой продукции.
Ввиду различной фактической влажности имеющихся в наличии песка и наполнителей указывать точное количество воды, необходимое для затворения раствора в ваших условиях, не представляется возможным.
В качестве наполнителя можно использовать как речной песок, так и отсев горнодобывающей промышленности. Использование отсева, ввиду его повышенной адгезивной активности, позволяет экономить 15-20% цемента.
Следует учитывать, что, в общем случае, песок должен включать в себя пески трех фракций в следующем соотношении:
— мелкий, но не пылевидный (0.3 — 1 мм) — 40%,
— средний (1 — 3 мм) — 30%,
— крупный (не более 5 мм) — 30%.
Фракция песка величиной до 5 мм обычно используется при изготовлении изделий толщиной 15-25 мм, а величиной до 10мм — для изделий толщиной 25-40 мм. Использование слишком мелкого песка не имеет смысла, так как это приводит к перерасходу цемента.
Изделия на основе белого портландцемента в случае использования в качестве наполнителя простого речного песка будут иметь желтоватый оттенок. Для изделий, которые должны быть окрашены в теплые и темные тона это вполне допустимо.
В то же время, в случае, когда требуется добиться правильной цветопередачи, вместо речного песка следует использовать кварцевый, так как он, в смеси с белым цементом, позволяет получать почти идеально белые поверхности.
Также, здесь необходимо отметить, что одним из преимуществ применения кварцевого песка вместо речного является то, что готовые изделия будут несколько прочнее.
Для снижения веса плиток искусственного камня в качестве заполнителя можно использовать перлит, пемзу, вспененное стекло или мелкий керамзит (фракции 1-5 мм), который является самым дешевым из числа, перечисленных выше.
Для увеличения прочности плиток искусственного камня, длина которых превышает их толщину более чем в 20 раз, имеет смысл добавлять в раствор фибрин.
Кроме этого, приемлемых результатов в плане увеличения прочности можно достигнуть путем добавления в раствор рубленного стекловолокна.
Одним из лучших и недорогих пластификаторов является хорошо всем известный «Суперпластификатор С-3». Данный пластификатор уже в количестве 0,2 — 0,7% от массы цемента позволяет получать самоуплотняющиеся, практически не требующие виброобработки бетонные смеси, а при снижении количества воды затворения — бетоны повышенной прочности при неизменной подвижности смеси. Вполне реально использовать оба эффекта одновременно, то есть получать смеси повышенной подвижности и одновременно с этим увеличивать прочность бетона за счет снижения количества воды в бетонном растворе.
Почти все из известных способов ускорения твердения цементных растворов путем введения в них различных добавок или обработки песка соляной кислотой, приводят к образованию солевых налетов на поверхности изделий, и, поэтому, применяются только при изготовлении конструкционных бетонов.
Наиболее приемлемым способом ускорения набора прочности декоративного искусственного камня является соблюдение температурно-влажностного режима.
Соотношения количества ингредиентов раствора
Универсального рецепта смеси не существует, поэтому, в общем случае, объемное соотношение количества цемента и песка зависит от требований к допустимой марке прочности изделий, от марки цемента, от фракции имеющегося в наличии песка и изменяется в пределах от 1:4 до 1:2. Объемное соотношение количества цемента и песка может достигать даже 1:1, например, когда требуется изготовить камень, покрытый трещинками, да еще и с выступающими гребнями.
В случае, когда продукция должна быть облегченная, например за счет добавления керамзита, тогда соотношение ингредиентов бетонной смеси по объему может быть следующим: 1 часть портландцемента М500; 0,5 части песка; 1-2,5 части керамзита (фракция 0-5 мм), вода до достижения необходимой консистенции (её количество зависит от уровня фактической влажности песка и керамзита). В теплое время года при изготовлении плиток большой площади с малой толщиной (с высоким риском разрушения), количество керамзита может достигать 2,5 частей, в холодное время года — его количество лучше держать на уровне 1 части.
Если Вы планируете использовать в качестве наполнителя бетона материалы, которые легче воды (пемза, вспученный перлит) — тогда смешивание раствора следует производить следующим образом: сначала производите смешивание сухих ингредиентов раствора, и только после этого добавляйте воду, при чем воды должно быть такое количество, что бы раствор был по возможности суше — иначе легкий наполнитель всплывет на поверхность.
Способы окрашивания искусственного камня
Окрашивание искусственного камня — это своего рода искусство. Однако, все же можно довольно четко выделить основные способы окрашивания искусственного камня:
1. Однотонным окрашиванием раствора.
2. Заполнением отдельных участков формы растворами, окрашенными в разные цвета (разные тона цвета).
3. Заполнением форм слабо перемешанной смесью из двух и более растворов, окрашенных в разные цвета (или разные тона цвета) — для получения «прожилок».
4. Нанесением красителей (сухих или жидких) на лицевую поверхность формы перед её заполнением раствором.
5. Окрашиванием поверхности камней после их выемки из формы.
6. Комбинированием вышеуказанных способов.
Каждый из вышеуказанных способов имеет свою область применения, но только их совместное комбинирование позволяет получить самые интересные эффекты.
Для окрашивания искусственного камня используют натуральные и синтетические пигменты, а также их смеси.
Натуральные пигменты — это различные окиси металлов, добываемые в рудниках. Синтетические обычно производят на основе солей железа из отходов сталелитейной продукции.
Обычно, для окрашивания растворов на основе портландцемента применяются следующие пигменты: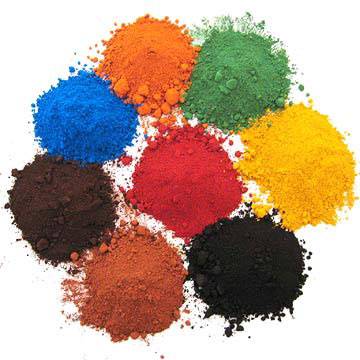
белый — двуокись титана;
желтый — желтая окись железа;
красный — красная окись железа;
черный — черная окись железа и сажа;
зеленый — зеленая окись хрома;
коричневый — коричневая окись железа и умбра.
Вышеуказанные пигменты нерастворимы в воде и окрашивают бетон, покрывая все ингредиенты раствора.
Интенсивность окраски поверхности зависит от многих параметров: количества пигмента в растворе, площади поверхности, эффективность процесса смешивания, фактуры поверхности и др.
Среднее количество пигмента в растворе составляет 5% при количестве цемента не более 10%. При такой дозировке проявляется небольшое увеличение времени твердения и незначительное снижение прочности бетона на сжатие.
При использовании пигментов для бетона следует учитывать то, что они различаются по своим физическим свойствам, в первую очередь по водопоглощению. Поэтому при приготовлении раствора может возникнуть необходимость откорректировать соотношение воды и цемента в растворе в соответствии с требованиями пигмента.
Пигменты следует дозировать по весу, а не по объему.
Здесь необходимо отметить, что одними из лучших считаются пигменты, которые производит концерн «Bayer».
Для поверхностной окраски камня рекомендуется использовать кислотные красители. Эти красители проникают внутрь поверхности, стойки к выцветанию, высыхают в период времени от нескольких часов до нескольких дней. Особенностью применения кислотных красителей является то, что их необходимо промывать водой или прочищать щеткой, устраняя излишки реакции красителя со щелочной средой бетона. После применения кислотных красителей поверхность бетонных изделий можно беспрепятственно обработать гидрофобизирующим средством для защиты от воздействия влаги.
Использовать быстровысыхающие краски на основе нитролаков и т.п. для окраски искусственного камня недопустимо, так как они создают тончайшую пленку, которая при любых перепадах температуры и влажности будет отслаиваться от поверхности камня.
Параметры изготовления камня
Бетонную смесь после укладки в формы с целью обеспечения высококачественного копирования фактуры её поверхности следует подвергнуть виброобработке.
Направление вибрации вибростола должно происходить в горизонтальной плоскости, но никак не в вертикальной.
Амплитуда вибрации должна быть порядка 0,15мм, а рекомендуемая частота вибрации в пределах 100-200 Гц.
Частота вибрации, превышающая оптимальную, ухудшает результаты обработки.
Длительность виброобработки определяется техноэкономическими соображениями, учитывая, что нарастание эффекта, достигаемого вибрированием, постепенно затухает.
При температуре 15-25°С и влажности воздуха 100% камень может набрать 90% прочности не ранее, чем через 7 дней. Если при том же уровне влажности температуру воздуха поднять до 60-80°С, тогда набор прочности до уровня 90% составит не менее 3-х дней.
Фактически, самым важным условием набора прочности является поддержание 100%-го уровня влажности. При таком уровне влажности отсутствуют условия для переноса влаги из изделий в воздух, поскольку парциальное давление паров на границе изделие-воздух в пропарочной камере равны между собой, и даже наоборот, влага из воздуха поглощается изделием и участвует в гидратации цемента.
При пониженной влажности воздуха она испаряется из изделия и не вступает в химическую реакцию, в результате изделие просто высыхает, так и не набрав положенной прочности. Учитывайте также и тот факт, что при температуре близкой к 0°С процесс твердения весьма замедляется.
Таким образом, в зависимости от Ваших условий Вы можете:
1) накрывать полиэтиленом палеты с готовой продукцией;
2) искусственно повышать уровень влажности воздуха в пропарочной камере (обязательно герметизируйте окна и двери во избежание сквозняков, увлажняйте полы и/или установите генератор «теплого водяного тумана»), в холодное время года поддерживайте температуру воздуха — не ниже 15°С.
Для получения продукции более высокого качества и снижения сроков набора прочности второй вариант является более приемлемым.
Предупреждение образования пор и раковин
Причиной появления пор на лицевой поверхности камня является воздух, который не оторвался от поверхности формы и не ушел в глубь раствора. Это может происходить по следующим причинам:
1. Бетонная смесь была слишком сухая. Как известно, чем жестче смесь, тем больше воздуха в ней содержится.
Если это так — добавьте пластификатор или отрегулируйте количество воды в растворе (первый вариант более приемлемый, так как прочность плитки будет выше).
2. Раствор был приготовлен в бетоно- растворосмесителе, который приводит к активному вовлечению воздуха в смесь и затворению в ней.
В данном случае наиболее пригодны к использованию смесители с принудительным смешиванием, которые перемешивают раствор, а не взбивают его, наполняя воздухом.
3. Форма изготовлена из материала, который плохо смачивается водой (например силиконовая форма) или форма была обработана разделительной смазкой.
Для повышения смачиваемости поверхности форм, обработанных смазкой, и, в итоге, для сокращения количества пор на лицевой поверхности готовых изделий, формы перед закладкой раствора следует слегка увлажнять водой с разведенным в ней поверхностно-активным веществом (например из пульверизатора). Излишек воды — не страшен, если он не повреждает предварительно нанесенную на поверхность формы цветовую маску. Простейшими поверхностно-активными веществами являются: мыльный раствор, моющие вещества для посуды и т.п.
4. Произведенная виброобработка смеси была недостаточной интенсивности и/или недостаточной по времени.
Тут, как, в общем-то и во всем остальном, — главное не переборщить, так как чрезмерная вибрация может привести к смазыванию рисунка, нанесенного на поверхность формы. Поэтому применяйте суперпластификаторы для бетона, отрегулируйте количество воды в растворе либо выбирайте формы для изготовления таких камней, где присутствие пузырьков на лицевой поверхности будет выглядеть обоснованным (например «старые кирпичи»).
Практически допустимым считается присутствие 2-3 капилярных отверстий на 1 кв. дециметр площади готового изделия.
Предупреждение образования солевого налета и способы его уменьшения
Белый налет на поверхности цементного камня — практически обыденная неприятность. Появление белого налета на бетонной поверхности принято подразделять на первичное — проявляется уже при твердении бетона, и вторичное — по мере его старения.
Свежеуложенный бетон пронизан системой капилляров, заполненных водным раствором продуктов гидратации цемента, по большей части гидрооксидом кальция. Когда поверхность бетона или хотя бы её участок покрыт пленкой воды, гидрооксид кальция может распространиться по всей поверхности камня, а затем, под действием содержащегося в атмосфере углекислого газа, образовать налет нерастворимого в воде карбоната кальция. Этот налет является первичным. Нерастворимость карбоната кальция является причиной постепенной остановки процесса его образования.
На лицевой поверхности искусственного камня, в отличие от его монтажной поверхности, первичный белый налет не появляется, так как в период твердения бетона она изолирована от атмосферы лицевой поверхностью формной оснастки.
Вторичное появление белого налета проявляется в процессе атмосферного старения бетона в виде осветления поверхности бетона, причиной которого является продолжение процесса гидратации компонентов раствора в затвердевшем материале и продолжается до тех пор, пока продолжается рост прочности бетона. Вторичное выцветание возможно, даже если бетон нормально затвердел и принудительное смачивание камня не приводит к появлению первичного высола. Процесс выцветания бетонного камня может проявляться на протяжении года после его изготовления. С течением времени карбонат кальция преобразовывается в бикарбонат, растворимый в воде, поэтому камень, установленный снаружи помещений, под действием дождей постепенно самоочищается и примерно через год восстанавливает свой изначальный цвет. Период времени, за который плитки самостоятельно восстановят свой первоначальный цвет зависит от климатических условий конкретной местности.
Повторное появление вторичного выцветания после естественного исчезновения налета проявляется довольно редко.
Первопричиной появления выцветания бетона является наличие гидрооксида кальция в цементном камне. Портландцемент и другие его виды на основе портландцементного клинкера в процессе гидратации образует гидроксид кальция в количестве до 15% от массы цемента.
Простейшим способом снижения образования белого налета является использование цементов с пониженным содержанием трехкальциевого силиката, но такие цементы характеризуются низкой скоростью твердения и пониженной маркой.
Следующим необходимым условием образования белого налета на поверхности бетона является наличие капилляров, по которым жидкая фаза цементного камня с растворенным в ней Са(ОН)2 выносится на поверхность изделия. Чтобы в затвердевшем бетоне не образовалась система взаимосвязанных пустот, по которым может перемещаться жидкая фаза, необходимо обеспечить достаточное количество цементного теста по отношению к объему песка.
Эта задача решается применением песка с оптимальным зерновым составом и небольшой удельной поверхностью (крупный песок). Капиллярные поры также возникают и при чрезмерном количестве воды в растворе, поэтому, чем суше раствор, тем ниже будет капиллярная пористость бетона. Но, в любом случае, полностью избавиться от капиллярных пор не удастся.
На появление белого налета также оказывают влияние и условия твердения бетона. Карбонизация поверхностного слоя бетонных изделий происходит в том случае, когда на их поверхности отсутствует водяная пленка, а в воздухе с влажностью 100% присутствует необходимое количество углекислого газа. При этом Са(ОН)2, растворенный в жидкости, заполняющей поры, переходит в нерастворимый карбонат кальция — СаСО2. Данный процесс проходит не в устьях, а внутри капилляров. Карбонат кальция кольматирует поры, повышая водонепроницаемость бетона, при чем не изменяя его цвета.
В целом для того, чтобы уменьшить образование белого налета на поверхности бетона, следует:
1) обеспечить его минимальную пористость и водопроницаемость;
2) в процессе твердения и при последующей выдержке на складе завода-изготовителя защищать поверхность изделий от прямого попадания влаги;
3) при твердении обеспечить доступ влажного воздуха (углекислого газа) к его поверхности.
Появление белого налета на поверхности бетонных изделий возможно предотвратить нанесением прозрачных поверхностных покрытий на кремнийорганической основе, которые создают на поверхности тончайшую прозрачную пленку, закрывающую поры бетона и предотвращающую выделение карбоната кальция на поверхность. Покрытие имеет малую толщину, поэтому срок его службы ограничен, но составляет не менее двух лет. С другой стороны, этого срока вполне достаточно, так как белый налет обычно образуется в течение первых двух лет. Пленка является газопроницаемой, поэтому слой бетона карбонизируется по описанной выше схеме, что служит гарантией от последующих высолов.
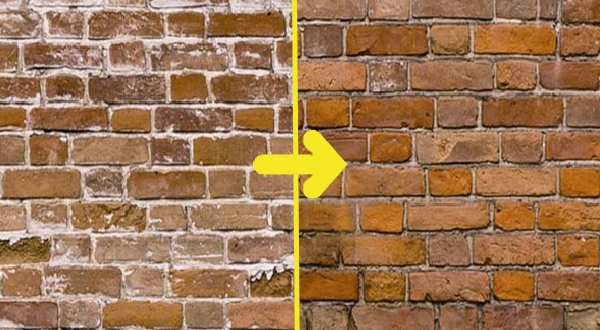
Искусственный камень — это современный декоративный облицовочный материал. Высокий спрос на него обусловлен следующими факторами:
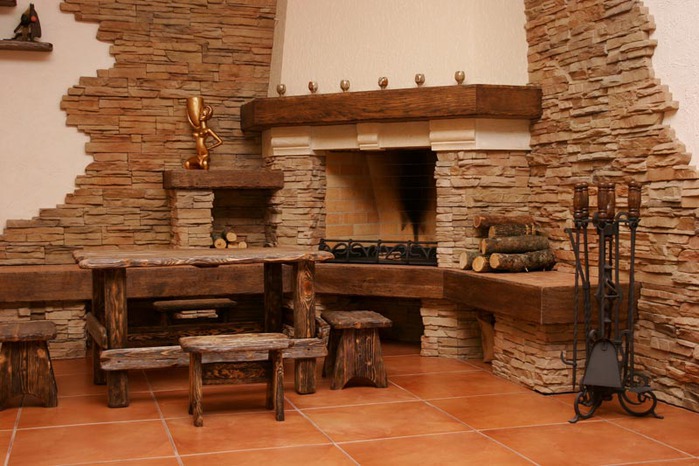
— высокие декоративные качества;
— простота и удобство укладки;
— огне- и влагостойкость;
— низкий вес (по сравнению с весом натуральных камней);
— низкая стоимость.
Искусственный камень не требует особого ухода и может прослужить без изменения цвета и фактуры не один десяток лет.
Применение современных технологий при производстве искусственного камня позволяет с удивительной точностью копировать фактуру гранита, базальта, песчаника, и других камней, изготавливать облицовочные плитки таких цветов и фактур, которые не существуют в природе.
Почти все оборудование, применяемое при изготовлении искусственного декоративного камня — такое же, как и при изготовлении тротуарной плитки (вибростолы, растворосмесители, весовое оборудование), за исключением одного — вместо жестких пластиковых применяются эластичные формы , которые являются ядром технологического процесса и самым важным производственным элементом.
Обычно облицовочные изделия из искусственного камня изготавливают размером — от 5 см2 до 0,5 м2 при толщине 1 — 2 см. В то же время плитки, имитирующие «булыжник» и «дикий камень», могут достигать толщины в 10 см.
В настоящее время искусственные камни изготавливаются в основном методами гиперпрессования, вибропрессования или вибролитья.
Данное руководство описывает процесс изготовления искусственных камней методом вибролитья, так как он, по сравнению с другими способами, позволяет изготавливать разнообразную продукцию высокого качества при сравнительно невысоких материальных затратах на организацию производства.
Ингредиенты бетонного раствора
Обычно состав бетонного раствора для изготовления искусственного камня включает в себя:
— портландцемент (белый или серый);
— вода;
— песок;
— различные наполнители;
— армирующие добавки;
— цветные пигменты;
— модификаторы (пластификаторы, ускорители твердения).
В большинстве случаев искусственный декоративный камень изготавливается на основе белого или серого портландцемента, что, в свою очередь, позволяет использовать такой камень для облицовки как внутренних, так и внешних поверхностей зданий и сооружений.
Нормальное твердение цемента происходит при температуре 15-20°С. Начало схватывания портландцемента должно наступать не ранее чем через 45 мин после затворения водой, а конец — не позже чем через 12 ч. При температуре от 0 до 5°С скорость набора прочности понижается в два-три раза, а при отрицательных температурах — почти полностью останавливается (так как вода переходит в кристаллическое состояние).
Прочность затворенного цемента нарастает неравномерно: за первые три дня она составляет 40-50% марки цемента, за 7 суток — 60-70% и только на 28-е сутки цемент набирает марочную прочность.
Белый портландцемент изготавливают путем измельчения белого маложелезистого клинкера, активной минеральной добавки и гипса.
Скорость твердения белого и цветных портландцементов несколько ниже, чем у обычных портландцементов, кроме этого у них повышенная усадка, пониженная морозостойкость и коррозионная устойчивость.
Вода — это то вещество, без которого увеличение прочности цементного камня невозможно. С другой стороны — излишнее количество воды, затворенное в растворе, отрицательно сказывается на прочностных характеристиках готовых изделий.
Поэтому при производстве искусственного камня следует, с одной стороны, обеспечить минимально возможное количество воды в растворе, а с другой стороны — создать необходимые условия для обеспечения процесса набора прочности готовой продукции.
Ввиду различной фактической влажности имеющихся в наличии песка и наполнителей указывать точное количество воды, необходимое для затворения раствора в ваших условиях, не представляется возможным.
В качестве наполнителя можно использовать как речной песок, так и отсев горнодобывающей промышленности. Использование отсева, ввиду его повышенной адгезивной активности, позволяет экономить 15-20% цемента.
Следует учитывать, что, в общем случае, песок должен включать в себя пески трех фракций в следующем соотношении:
— мелкий, но не пылевидный (0.3 — 1 мм) — 40%,
— средний (1 — 3 мм) — 30%,
— крупный (не более 5 мм) — 30%.
Фракция песка величиной до 5 мм обычно используется при изготовлении изделий толщиной 15-25 мм, а величиной до 10мм — для изделий толщиной 25-40 мм. Использование слишком мелкого песка не имеет смысла, так как это приводит к перерасходу цемента.
Изделия на основе белого портландцемента в случае использования в качестве наполнителя простого речного песка будут иметь желтоватый оттенок. Для изделий, которые должны быть окрашены в теплые и темные тона это вполне допустимо.
В то же время, в случае, когда требуется добиться правильной цветопередачи, вместо речного песка следует использовать кварцевый, так как он, в смеси с белым цементом, позволяет получать почти идеально белые поверхности.
Также, здесь необходимо отметить, что одним из преимуществ применения кварцевого песка вместо речного является то, что готовые изделия будут несколько прочнее.
Для снижения веса плиток искусственного камня в качестве заполнителя можно использовать перлит, пемзу, вспененное стекло или мелкий керамзит (фракции 1-5 мм), который является самым дешевым из числа, перечисленных выше.
Для увеличения прочности плиток искусственного камня, длина которых превышает их толщину более чем в 20 раз, имеет смысл добавлять в раствор фибрин.
Кроме этого, приемлемых результатов в плане увеличения прочности можно достигнуть путем добавления в раствор рубленного стекловолокна.
Одним из лучших и недорогих пластификаторов является хорошо всем известный «Суперпластификатор С-3». Данный пластификатор уже в количестве 0,2 — 0,7% от массы цемента позволяет получать самоуплотняющиеся, практически не требующие виброобработки бетонные смеси, а при снижении количества воды затворения — бетоны повышенной прочности при неизменной подвижности смеси. Вполне реально использовать оба эффекта одновременно, то есть получать смеси повышенной подвижности и одновременно с этим увеличивать прочность бетона за счет снижения количества воды в бетонном растворе.
Почти все из известных способов ускорения твердения цементных растворов путем введения в них различных добавок или обработки песка соляной кислотой, приводят к образованию солевых налетов на поверхности изделий, и, поэтому, применяются только при изготовлении конструкционных бетонов.
Наиболее приемлемым способом ускорения набора прочности декоративного искусственного камня является соблюдение температурно-влажностного режима.
Соотношения количества ингредиентов раствора
Универсального рецепта смеси не существует, поэтому, в общем случае, объемное соотношение количества цемента и песка зависит от требований к допустимой марке прочности изделий, от марки цемента, от фракции имеющегося в наличии песка и изменяется в пределах от 1:4 до 1:2. Объемное соотношение количества цемента и песка может достигать даже 1:1, например, когда требуется изготовить камень, покрытый трещинками, да еще и с выступающими гребнями.
В случае, когда продукция должна быть облегченная, например за счет добавления керамзита, тогда соотношение ингредиентов бетонной смеси по объему может быть следующим: 1 часть портландцемента М500; 0,5 части песка; 1-2,5 части керамзита (фракция 0-5 мм), вода до достижения необходимой консистенции (её количество зависит от уровня фактической влажности песка и керамзита). В теплое время года при изготовлении плиток большой площади с малой толщиной (с высоким риском разрушения), количество керамзита может достигать 2,5 частей, в холодное время года — его количество лучше держать на уровне 1 части.
Если Вы планируете использовать в качестве наполнителя бетона материалы, которые легче воды (пемза, вспученный перлит) — тогда смешивание раствора следует производить следующим образом: сначала производите смешивание сухих ингредиентов раствора, и только после этого добавляйте воду, при чем воды должно быть такое количество, что бы раствор был по возможности суше — иначе легкий наполнитель всплывет на поверхность.
Способы окрашивания искусственного камня
Окрашивание искусственного камня — это своего рода искусство. Однако, все же можно довольно четко выделить основные способы окрашивания искусственного камня:
1. Однотонным окрашиванием раствора.
2. Заполнением отдельных участков формы растворами, окрашенными в разные цвета (разные тона цвета).
3. Заполнением форм слабо перемешанной смесью из двух и более растворов, окрашенных в разные цвета (или разные тона цвета) — для получения «прожилок».
4. Нанесением красителей (сухих или жидких) на лицевую поверхность формы перед её заполнением раствором.
5. Окрашиванием поверхности камней после их выемки из формы.
6. Комбинированием вышеуказанных способов.
Каждый из вышеуказанных способов имеет свою область применения, но только их совместное комбинирование позволяет получить самые интересные эффекты.
Для окрашивания искусственного камня используют натуральные и синтетические пигменты, а также их смеси.
Натуральные пигменты — это различные окиси металлов, добываемые в рудниках. Синтетические обычно производят на основе солей железа из отходов сталелитейной продукции.
Обычно, для окрашивания растворов на основе портландцемента применяются следующие пигменты:
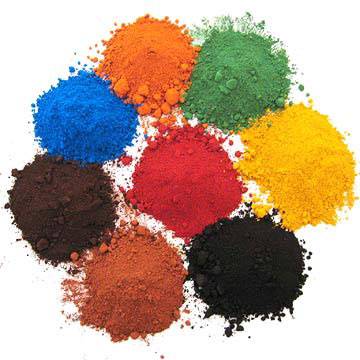
белый — двуокись титана;
желтый — желтая окись железа;
красный — красная окись железа;
черный — черная окись железа и сажа;
зеленый — зеленая окись хрома;
коричневый — коричневая окись железа и умбра.
Вышеуказанные пигменты нерастворимы в воде и окрашивают бетон, покрывая все ингредиенты раствора.
Интенсивность окраски поверхности зависит от многих параметров: количества пигмента в растворе, площади поверхности, эффективность процесса смешивания, фактуры поверхности и др.
Среднее количество пигмента в растворе составляет 5% при количестве цемента не более 10%. При такой дозировке проявляется небольшое увеличение времени твердения и незначительное снижение прочности бетона на сжатие.
При использовании пигментов для бетона следует учитывать то, что они различаются по своим физическим свойствам, в первую очередь по водопоглощению. Поэтому при приготовлении раствора может возникнуть необходимость откорректировать соотношение воды и цемента в растворе в соответствии с требованиями пигмента.
Пигменты следует дозировать по весу, а не по объему.
Здесь необходимо отметить, что одними из лучших считаются пигменты, которые производит концерн «Bayer».
Для поверхностной окраски камня рекомендуется использовать кислотные красители. Эти красители проникают внутрь поверхности, стойки к выцветанию, высыхают в период времени от нескольких часов до нескольких дней. Особенностью применения кислотных красителей является то, что их необходимо промывать водой или прочищать щеткой, устраняя излишки реакции красителя со щелочной средой бетона. После применения кислотных красителей поверхность бетонных изделий можно беспрепятственно обработать гидрофобизирующим средством для защиты от воздействия влаги.
Использовать быстровысыхающие краски на основе нитролаков и т.п. для окраски искусственного камня недопустимо, так как они создают тончайшую пленку, которая при любых перепадах температуры и влажности будет отслаиваться от поверхности камня.
Параметры изготовления камня
Бетонную смесь после укладки в формы с целью обеспечения высококачественного копирования фактуры её поверхности следует подвергнуть виброобработке.
Направление вибрации вибростола должно происходить в горизонтальной плоскости, но никак не в вертикальной.
Амплитуда вибрации должна быть порядка 0,15мм, а рекомендуемая частота вибрации в пределах 100-200 Гц.
Частота вибрации, превышающая оптимальную, ухудшает результаты обработки.
Длительность виброобработки определяется техноэкономическими соображениями, учитывая, что нарастание эффекта, достигаемого вибрированием, постепенно затухает.
При температуре 15-25°С и влажности воздуха 100% камень может набрать 90% прочности не ранее, чем через 7 дней. Если при том же уровне влажности температуру воздуха поднять до 60-80°С, тогда набор прочности до уровня 90% составит не менее 3-х дней.
Фактически, самым важным условием набора прочности является поддержание 100%-го уровня влажности. При таком уровне влажности отсутствуют условия для переноса влаги из изделий в воздух, поскольку парциальное давление паров на границе изделие-воздух в пропарочной камере равны между собой, и даже наоборот, влага из воздуха поглощается изделием и участвует в гидратации цемента.
При пониженной влажности воздуха она испаряется из изделия и не вступает в химическую реакцию, в результате изделие просто высыхает, так и не набрав положенной прочности. Учитывайте также и тот факт, что при температуре близкой к 0°С процесс твердения весьма замедляется.
Таким образом, в зависимости от Ваших условий Вы можете:
1) накрывать полиэтиленом палеты с готовой продукцией;
2) искусственно повышать уровень влажности воздуха в пропарочной камере (обязательно герметизируйте окна и двери во избежание сквозняков, увлажняйте полы и/или установите генератор «теплого водяного тумана»), в холодное время года поддерживайте температуру воздуха — не ниже 15°С.
Для получения продукции более высокого качества и снижения сроков набора прочности второй вариант является более приемлемым.
Предупреждение образования пор и раковин
Причиной появления пор на лицевой поверхности камня является воздух, который не оторвался от поверхности формы и не ушел в глубь раствора. Это может происходить по следующим причинам:
1. Бетонная смесь была слишком сухая. Как известно, чем жестче смесь, тем больше воздуха в ней содержится.
Если это так — добавьте пластификатор или отрегулируйте количество воды в растворе (первый вариант более приемлемый, так как прочность плитки будет выше).
2. Раствор был приготовлен в бетоно- растворосмесителе, который приводит к активному вовлечению воздуха в смесь и затворению в ней.
В данном случае наиболее пригодны к использованию смесители с принудительным смешиванием, которые перемешивают раствор, а не взбивают его, наполняя воздухом.
3. Форма изготовлена из материала, который плохо смачивается водой (например силиконовая форма) или форма была обработана разделительной смазкой.
Для повышения смачиваемости поверхности форм, обработанных смазкой, и, в итоге, для сокращения количества пор на лицевой поверхности готовых изделий, формы перед закладкой раствора следует слегка увлажнять водой с разведенным в ней поверхностно-активным веществом (например из пульверизатора). Излишек воды — не страшен, если он не повреждает предварительно нанесенную на поверхность формы цветовую маску. Простейшими поверхностно-активными веществами являются: мыльный раствор, моющие вещества для посуды и т.п.
4. Произведенная виброобработка смеси была недостаточной интенсивности и/или недостаточной по времени.
Тут, как, в общем-то и во всем остальном, — главное не переборщить, так как чрезмерная вибрация может привести к смазыванию рисунка, нанесенного на поверхность формы. Поэтому применяйте суперпластификаторы для бетона, отрегулируйте количество воды в растворе либо выбирайте формы для изготовления таких камней, где присутствие пузырьков на лицевой поверхности будет выглядеть обоснованным (например «старые кирпичи»).
Практически допустимым считается присутствие 2-3 капилярных отверстий на 1 кв. дециметр площади готового изделия.
Предупреждение образования солевого налета и способы его уменьшения
Белый налет на поверхности цементного камня — практически обыденная неприятность. Появление белого налета на бетонной поверхности принято подразделять на первичное — проявляется уже при твердении бетона, и вторичное — по мере его старения.
Свежеуложенный бетон пронизан системой капилляров, заполненных водным раствором продуктов гидратации цемента, по большей части гидрооксидом кальция. Когда поверхность бетона или хотя бы её участок покрыт пленкой воды, гидрооксид кальция может распространиться по всей поверхности камня, а затем, под действием содержащегося в атмосфере углекислого газа, образовать налет нерастворимого в воде карбоната кальция. Этот налет является первичным. Нерастворимость карбоната кальция является причиной постепенной остановки процесса его образования.
На лицевой поверхности искусственного камня, в отличие от его монтажной поверхности, первичный белый налет не появляется, так как в период твердения бетона она изолирована от атмосферы лицевой поверхностью формной оснастки.
Вторичное появление белого налета проявляется в процессе атмосферного старения бетона в виде осветления поверхности бетона, причиной которого является продолжение процесса гидратации компонентов раствора в затвердевшем материале и продолжается до тех пор, пока продолжается рост прочности бетона. Вторичное выцветание возможно, даже если бетон нормально затвердел и принудительное смачивание камня не приводит к появлению первичного высола. Процесс выцветания бетонного камня может проявляться на протяжении года после его изготовления. С течением времени карбонат кальция преобразовывается в бикарбонат, растворимый в воде, поэтому камень, установленный снаружи помещений, под действием дождей постепенно самоочищается и примерно через год восстанавливает свой изначальный цвет. Период времени, за который плитки самостоятельно восстановят свой первоначальный цвет зависит от климатических условий конкретной местности.
Повторное появление вторичного выцветания после естественного исчезновения налета проявляется довольно редко.
Первопричиной появления выцветания бетона является наличие гидрооксида кальция в цементном камне. Портландцемент и другие его виды на основе портландцементного клинкера в процессе гидратации образует гидроксид кальция в количестве до 15% от массы цемента.
Простейшим способом снижения образования белого налета является использование цементов с пониженным содержанием трехкальциевого силиката, но такие цементы характеризуются низкой скоростью твердения и пониженной маркой.
Следующим необходимым условием образования белого налета на поверхности бетона является наличие капилляров, по которым жидкая фаза цементного камня с растворенным в ней Са(ОН)2 выносится на поверхность изделия. Чтобы в затвердевшем бетоне не образовалась система взаимосвязанных пустот, по которым может перемещаться жидкая фаза, необходимо обеспечить достаточное количество цементного теста по отношению к объему песка.
Эта задача решается применением песка с оптимальным зерновым составом и небольшой удельной поверхностью (крупный песок). Капиллярные поры также возникают и при чрезмерном количестве воды в растворе, поэтому, чем суше раствор, тем ниже будет капиллярная пористость бетона. Но, в любом случае, полностью избавиться от капиллярных пор не удастся.
На появление белого налета также оказывают влияние и условия твердения бетона. Карбонизация поверхностного слоя бетонных изделий происходит в том случае, когда на их поверхности отсутствует водяная пленка, а в воздухе с влажностью 100% присутствует необходимое количество углекислого газа. При этом Са(ОН)2, растворенный в жидкости, заполняющей поры, переходит в нерастворимый карбонат кальция — СаСО2. Данный процесс проходит не в устьях, а внутри капилляров. Карбонат кальция кольматирует поры, повышая водонепроницаемость бетона, при чем не изменяя его цвета.
В целом для того, чтобы уменьшить образование белого налета на поверхности бетона, следует:
1) обеспечить его минимальную пористость и водопроницаемость;
2) в процессе твердения и при последующей выдержке на складе завода-изготовителя защищать поверхность изделий от прямого попадания влаги;
3) при твердении обеспечить доступ влажного воздуха (углекислого газа) к его поверхности.
Появление белого налета на поверхности бетонных изделий возможно предотвратить нанесением прозрачных поверхностных покрытий на кремнийорганической основе, которые создают на поверхности тончайшую прозрачную пленку, закрывающую поры бетона и предотвращающую выделение карбоната кальция на поверхность. Покрытие имеет малую толщину, поэтому срок его службы ограничен, но составляет не менее двух лет. С другой стороны, этого срока вполне достаточно, так как белый налет обычно образуется в течение первых двух лет. Пленка является газопроницаемой, поэтому слой бетона карбонизируется по описанной выше схеме, что служит гарантией от последующих высолов.
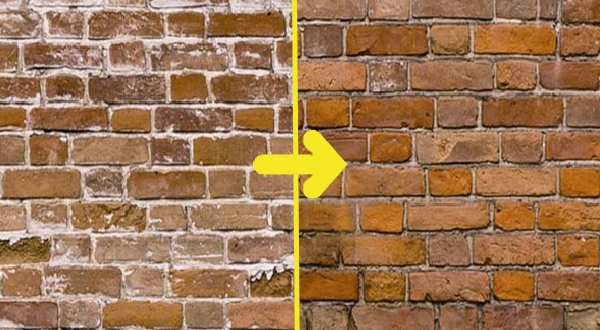